CNC aluminum machining has revolutionized the manufacturing landscape, offering precision and efficiency for a variety of applications. This process involves using computer numerical control technology to shape and cut aluminum with remarkable accuracy. Understanding CNC aluminum is crucial for industries looking to optimize production and improve product quality, making it a topic worth exploring.
What Is CNC Aluminum
CNC aluminum refers to the process of using computer numerical control (CNC) technology to machine aluminum parts and components. This technology facilitates precise cutting, shaping, and finishing of aluminum materials, ensuring consistent quality and accuracy.
CNC machining utilizes specialized software that directs the machine’s movements. Operators input designs created with CAD (computer-aided design) software, which the CNC machine then interprets. As a result, manufacturers can produce complex shapes and intricate designs that would be difficult or impossible to achieve through manual processes.
Aluminum is a favored material in many industries due to its lightweight properties, corrosion resistance, and excellent machinability. Applications of CNC aluminum machining include aerospace components, automotive parts, and electronic housings, underscoring its importance in modern manufacturing.
Importance of aluminum CNC machining lies in its efficiency and repeatability. The process reduces waste by optimizing material usage, while also minimizing production time, which enhances overall productivity. By leveraging CNC technology, businesses can achieve higher precision and lower costs in their manufacturing processes.
Benefits of CNC Aluminum
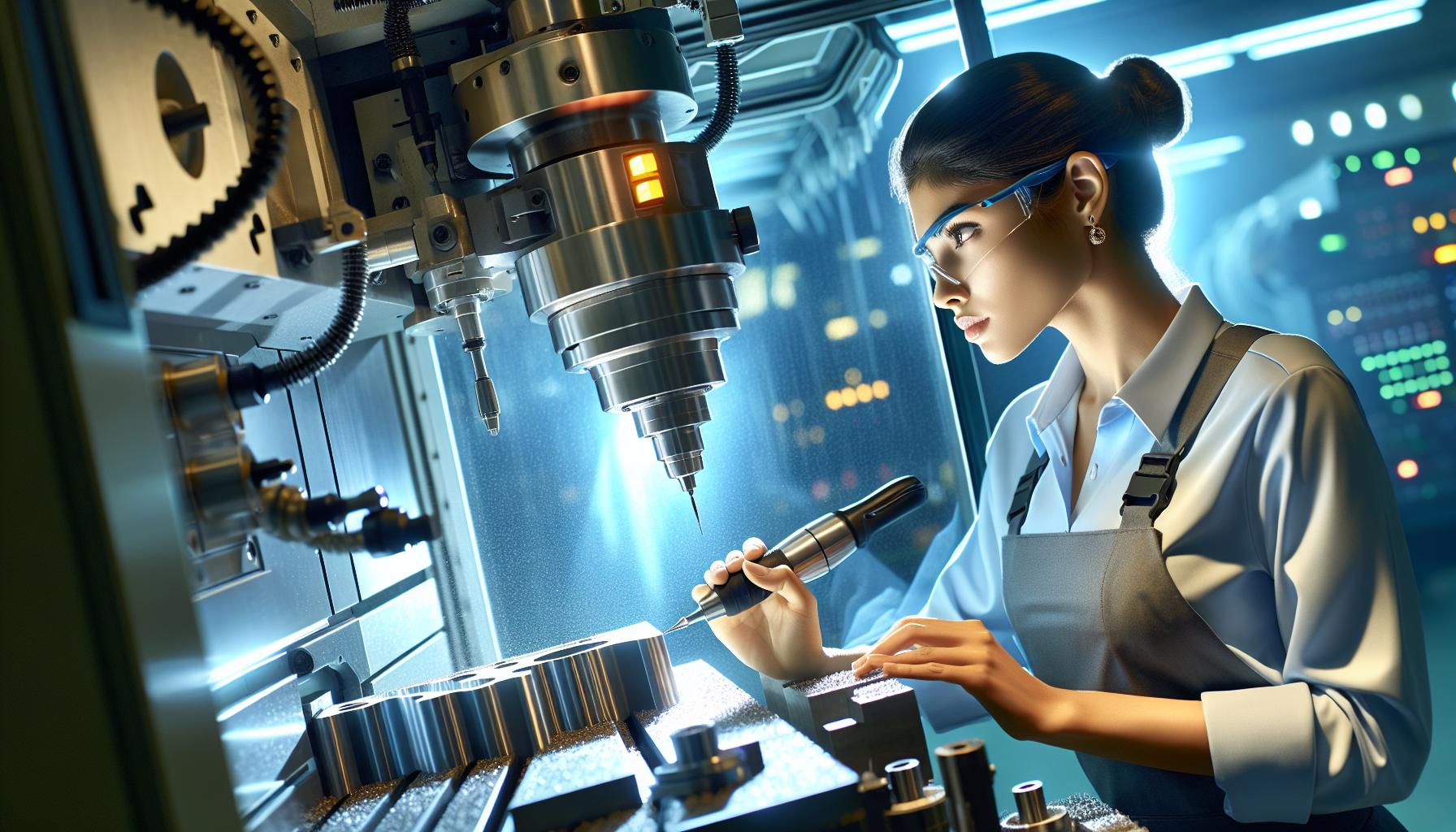
CNC aluminum machining offers several advantages that improve efficiency and product quality in manufacturing processes.
Precision and Accuracy
CNC aluminum ensures high precision in production. Computer numerical control technology allows for exact measurements and repeatable manufacturing processes. The use of CAD software contributes to accurate interpretation of designs, minimizing errors in machining. This precision is crucial for industries that require intricate and detailed components, such as aerospace and electronics.
Durability and Strength
CNC aluminum parts exhibit significant durability and strength. Aluminum’s inherent properties, combined with precise machining, lead to components that withstand demanding applications. The strength-to-weight ratio of aluminum makes it an ideal material for lightweight structures while maintaining structural integrity. This quality is especially important in industries like automotive, where performance and safety rely on robust materials.
Applications of CNC Aluminum
CNC aluminum machining finds extensive use across multiple industries due to its precision, efficiency, and versatility.
Aerospace Industry
CNC aluminum plays a critical role in aerospace manufacturing. It produces lightweight components that meet strict safety and performance standards. Parts like brackets, housings, and wing structures benefit from aluminum’s strength-to-weight ratio, reducing fuel consumption and enhancing aircraft efficiency.
Automotive Industry
CNC aluminum machining significantly impacts the automotive sector. It is used to manufacture parts such as engine blocks, transmission cases, and decorative trim pieces. The lightweight nature of aluminum helps improve vehicle performance, fuel efficiency, and compliance with environmental regulations, while the precision offered by CNC technology ensures optimal fit and function.
Consumer Products
CNC aluminum machining is essential for creating consumer products, ranging from electronics casings to kitchen appliances. High-quality aluminum parts make devices more durable and aesthetically pleasing. CNC machining allows for customization, enabling manufacturers to meet specific design requirements and consumer preferences while maintaining consistent quality across production runs.
The CNC Machining Process
CNC machining involves a series of precise steps to transform aluminum materials into finished parts. The process includes design, machining, and finishing, focusing on achieving accuracy and quality.
Design and Prototyping
Design and prototyping stage utilizes computer-aided design (CAD) software, allowing engineers to create detailed blueprints of parts. These designs define dimensions, tolerances, and surface finishes. Prototyping follows design, enabling testing and adjustments before final production. This stage ensures that any design flaws are identified and corrected, minimizing errors in later stages.
Machining Techniques
Machining techniques vary based on the requirements of the part. Common methods include milling, turning, and drilling.
- Milling: Involves rotating cutting tools to remove material from the aluminum workpiece, creating complex shapes and features.
- Turning: Utilizes a lathe to spin the aluminum block while a cutting tool shapes the material, ideal for cylindrical parts.
- Drilling: Employs drill bits to create holes in aluminum components, essential for assembly and functionality.
These techniques allow for high precision and adaptability in producing various component geometries.
Finishing Processes
Finishing processes improve the quality and appearance of CNC machined aluminum parts. Common finishing methods include anodizing, powder coating, and grinding.
- Anodizing: Involves electrochemically treating aluminum to create a durable, protective oxide layer that improves corrosion resistance.
- Powder Coating: Applies a colored powder that is baked onto the surface, providing a robust finish available in multiple colors.
- Grinding: Involves refining surfaces to achieve a specific smoothness or tolerance, important in applications requiring tight specifications.
These finishing techniques not only improve aesthetics but also improve the durability and performance of the components.
Conclusion
CNC aluminum machining stands as a transformative force in modern manufacturing. By leveraging advanced technology, it enables industries to achieve unparalleled precision and efficiency in producing aluminum components. The ability to create complex designs with minimal waste not only enhances productivity but also drives down costs.
As industries continue to prioritize quality and performance, understanding the value of CNC aluminum becomes increasingly essential. Its applications across sectors like aerospace, automotive, and consumer goods underscore its significance. Embracing CNC aluminum machining can lead to innovative solutions and improved product outcomes, positioning businesses for success in a competitive landscape.
Frequently Asked Questions
What is CNC aluminum machining?
CNC aluminum machining refers to the use of computer numerical control (CNC) technology to cut, shape, and finish aluminum parts accurately. This process utilizes specialized software to interpret designs created with computer-aided design (CAD) software, allowing for high precision and consistency in producing complex components.
What are the advantages of CNC aluminum machining?
The advantages of CNC aluminum machining include high precision, efficiency, and repeatability, which reduce material waste and production time. It enhances productivity, lowers costs, and ensures high-quality production due to minimized errors and optimized designs. Additionally, CNC parts are durable and lightweight, ideal for various applications.
Which industries benefit from CNC aluminum machining?
CNC aluminum machining is beneficial in multiple industries, including aerospace, automotive, and electronics. It produces lightweight components that meet strict safety standards in aerospace, improves performance in automotive, and enhances product customization in consumer electronics, thus maintaining high-quality standards.
How does the CNC machining process work?
The CNC machining process involves several steps: design, machining, and finishing. It begins with creating detailed blueprints using CAD software, followed by machining techniques like milling and drilling. Finally, finishing processes, such as anodizing or grinding, enhance the quality and appearance of the aluminum parts.
Why is aluminum a preferred material for machining?
Aluminum is preferred for machining due to its lightweight properties, corrosion resistance, and excellent machinability. Its favorable strength-to-weight ratio makes it ideal for applications requiring both robustness and reduced weight, especially in industries such as automotive and aerospace.