Key Takeaways
- Interlocking brick machines enhance construction efficiency by enabling on-site production of uniform, mortarless bricks, leading to faster project completion and reduced labor costs.
- These machines support sustainability by using local materials, minimizing waste, and reducing the need for water and mortar, aligning with eco-friendly construction trends.
- With options ranging from manual to fully automatic models, interlocking brick machines cater to small, medium, and large-scale projects, offering various output capacities and automation levels.
- Bricks produced by interlocking machines are known for their high compressive strength and precise dimensions, resulting in stronger, more stable, and better-aligned structures.
- Routine maintenance and reliable after-sales support are crucial for maximizing machine uptime and longevity, making manufacturer service and warranty considerations essential for buyers.
- Leading brands like Lontto provide Chicago contractors with a diverse selection of interlocking brick machines, operator training, and local technical support, ensuring optimal performance and value.
Interlocking brick machines produce precision-engineered bricks with edges that fit together without mortar, revolutionising construction efficiency and sustainability. These machines use hydraulic or mechanical compaction to create uniform blocks with consistent density and strength from locally-sourced materials. Production capacities range from 2,000 to 7,200 bricks per eight-hour shift depending on automation levels. Leading manufacturers like Block Machine Lontto offer comprehensive solutions from manual to fully automatic systems with installation support and operator training.
What Is an Interlocking Brick Machine?
An interlocking brick machine forms bricks with precise edges that allow them to lock together firmly without mortar. The equipment uses hydraulic or mechanical compaction to ensure consistent block density and strength. Operators feed raw material—typically a mix of sand, cement, and aggregate—into the mold, then the machine compresses the mixture to create bricks with uniform dimensions. Lontto manufactures fully automatic and manual interlocking brick machines suitable for urban development projects in Chicago and globally. Typical machines from Lontto output between 2,000 and 7,200 bricks per 8-hour shift, depending on the model, such as LT2-40 and M7MI Twin. Design features like mold exchange systems and energy-efficient hydraulic components support faster production with lower material waste. Interlocking bricks produced by these machines allow faster site assembly, reduce labor reliance, and improve wall alignment. This technology also supports sustainable building by reducing mortar usage and construction debris. For construction companies in Chicago, Lontto’s localized support streamlines equipment commissioning and operator training, increasing operational uptime.
Key Features of Interlocking Brick Machines
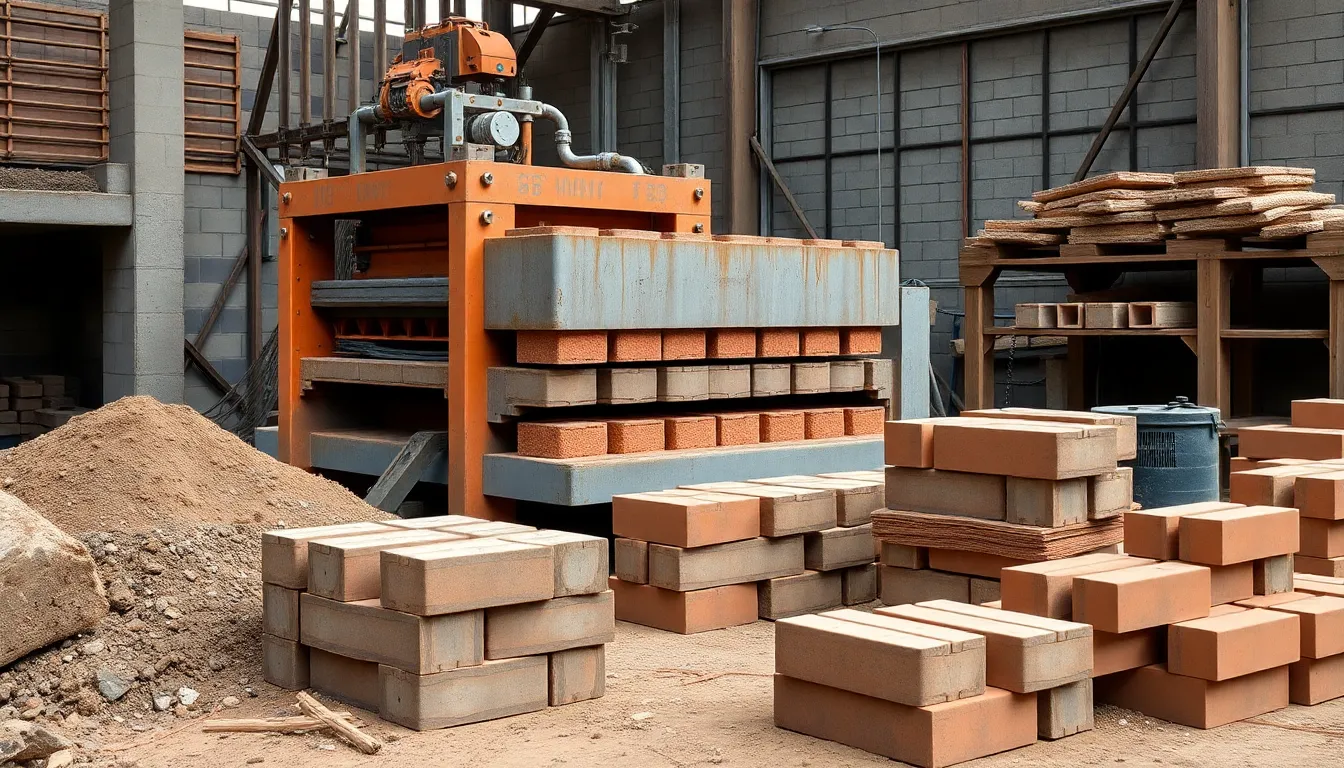
Interlocking brick machines combine precision engineering and robust build quality to support efficient construction workflows. These machines give construction teams the ability to produce load-bearing, interlocking bricks directly on-site, minimizing waste and speeding up installation on Chicago-area building projects.
Types of Interlocking Brick Machines
Manual and semi-automatic interlocking brick machines need operator input for shaping and compacting bricks, meeting small to mid-range project needs. Fully automatic machines use digital controls to deliver high volumes with minimal labor, ideal for continuous production cycles. Double cavity models feature two brick-forming cavities, allowing operators to make hollow, solid, or specialty interlocking bricks in a single cycle. Hydraulic press machines use high-pressure hydraulic systems to create consistent shape and durable strength, with options for plug-and-play integration on most Chicago sites. Lontto supports manual, semi-automatic, and automatic machines, offering installation assistance and training for US construction firms.
Materials Used in Brick Production
Interlocking brick machines process stone powder, fly ash, sand, gravel, soil, cement, and water, creating bricks suited for diverse site conditions. Typical mixes for clay interlocking bricks use 50-60% clay, 10-15% cement, and 20-30% sand, with water proportions adjusted for moisture content. Fly ash and lime components strengthen unburned bricks for exterior landscaping, paving, or structural retaining walls. Chicago construction projects using Lontto’s hydraulic or double cavity machines benefit from raw material flexibility, adapting recipes to meet local code, soil, and weather requirements while reducing environmental impact.
Benefits of Using Interlocking Brick Machines
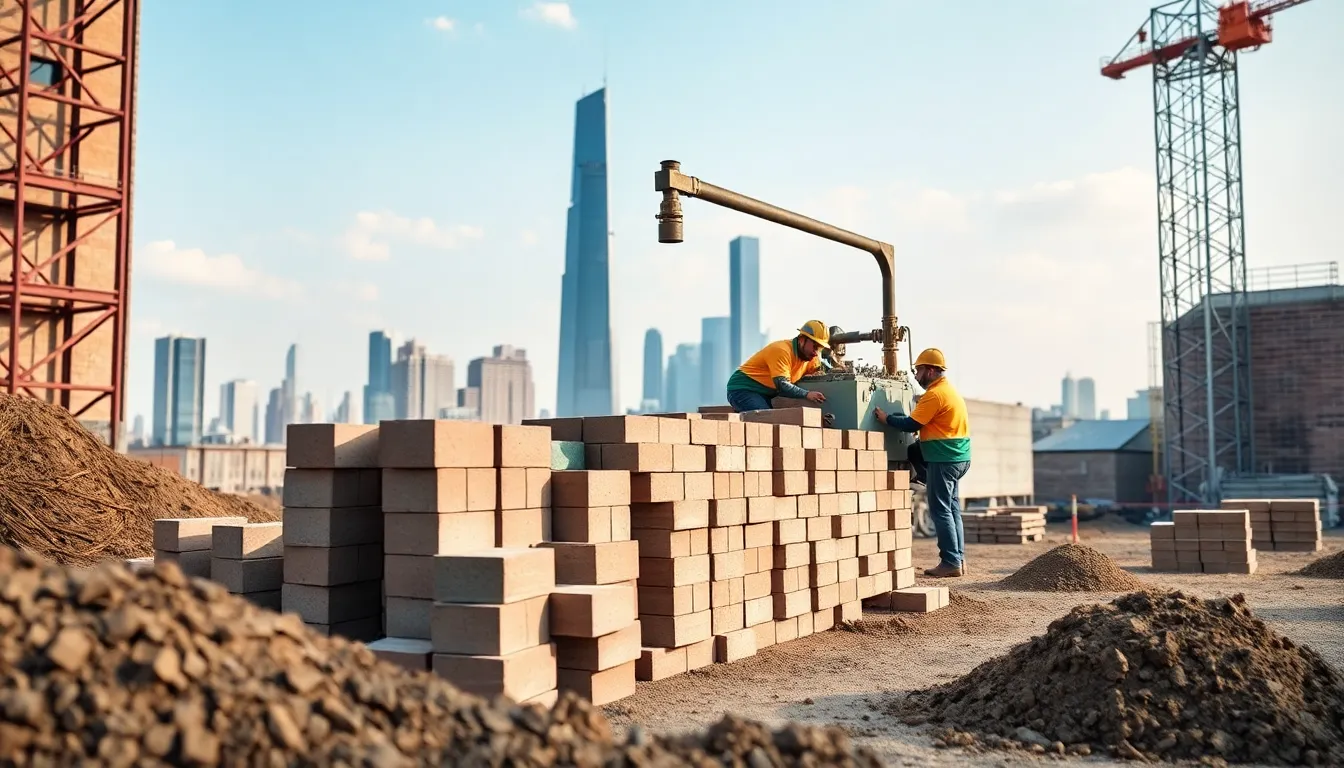
Interlocking brick machines support fast, efficient, and environmentally responsible construction. Lontto supplies solutions in Chicago, making these benefits accessible on-site for large and small projects.
Cost-Effectiveness and Efficiency
Interlocking brick machines cut project costs by removing the need for mortar and reducing labor. Automated models, like Lontto’s fully automatic units, allow for output of up to 7,200 bricks in one shift, matching tight schedules in Chicago construction. Uniform bricks increase structural stability and speed up assembly, minimizing rework. The modular mold exchange system further improves flexibility and keeps downtime low. For projects with limited labor or time-sensitive demands, these machines lower expenses while ensuring consistent quality.
Environmental Impact
Brick machines support sustainable construction by maximizing the use of local materials such as clay, soil, and fly ash. The dry stacking method made possible by interlocking bricks reduces the need for water and mortar, preserving natural resources. Lontto’s equipment minimizes waste by producing only the required quantity, and the bricks’ durability decreases long-term replacements. The use of regionally available materials in Chicago projects limits transportation emissions. Every production and installation step focuses on resource conservation and waste reduction.
Performance and Output Quality
Interlocking brick machines consistently deliver high output rates and precise brick dimensions. In brick production lines, Lontto machines achieve between 500 and 3,600 bricks per hour depending on automation level and model. Hydraulic compaction and advanced molds maintain tight tolerances, ensuring every unit matches specified quality requirements.
Durability and Strength of Bricks
Bricks from interlocking brick machines show high compressive strength levels and improved seismic resistance. Research attributes this to the lack of mortar joints and precise interlocking shapes formed during manufacturing, adding greater load distribution. Buildings constructed with these bricks gain improved structural alignment and mechanical stability, especially under lateral forces. Trials using Lontto equipment confirm that integrating additives—like fly ash or marble powder—can increase durability while still meeting strength benchmarks if additives are kept within recommended proportions. Brick longevity depends on consistent shape, surface quality, and the machine’s production tolerances.
Automation and User-Friendliness
Lontto fully automatic hydraulic machines reduce required labor to 2–4 operators by automating feeding, molding, compression, and delivery. This limits manual intervention and increases batch consistency. Control systems with electrical and hydraulic components ensure uniform brick size and reduce human error during continuous operation. Lontto’s machines offer one-touch operation, straightforward maintenance steps, and stable functioning on multiple terrains. Chicago construction crews using these machines benefit from local Lontto service support, which streamlines operator training and machine commissioning, increasing efficiency and reliability. Multipurpose molds expand usability for colored, erosion-resistant, or specialty brick types.
Considerations Before Purchasing
Interlocking brick machine buyers compare key specifications and support options to match project demands. Lontto provides both manual and automatic models for Chicago contractors seeking reliable installation, warranty, and operator training.
Price Comparison
Price differences between interlocking brick machines depend on automation, output, and brand reputation. Manual models cost $1,500–$3,500 for basic units with low hourly production, such as 100–500 bricks. Higher-capacity manual and semi-automatic machines range from $3,500–$6,000 and deliver 500–1,000 bricks per hour, meeting requirements for medium jobsites or small builders. Fully automatic machines, priced from $6,000 up to $10,000, feature PLC systems and continuous conveyors, producing over 7,000 bricks in an 8-hour shift. Chicago buyers select Lontto automatic machines for large commercial installations where high throughput and reduced labor matter. Warranty, local service, and after-sales support contribute to total ownership cost.
Type | Price Range (USD) | Production Capability | Suitable For |
---|---|---|---|
Manual | $1,500–$3,500 | 100–500 bricks/hr | Small projects |
Semi-Automatic | $3,500–$6,000 | 500–1,000 bricks/hr | Medium sites |
Fully Automatic | $6,000–$10,000+ | 7,000+ bricks/8 hr shift | Commercial operations |
Maintenance and Support
Interlocking brick machines require regular maintenance for hydraulic pumps, electrical parts, and pressing molds to keep performance steady. Lontto offers Chicago customers technical support, operator training, and fast replacement parts to minimize downtime. Automated models simplify diagnostics through integrated control panels, letting operators identify faults quickly. A comprehensive service agreement covers scheduled inspection, cleaning, and system calibration. Buyers check warranty lengths and local support options before purchasing, since post-sale assistance impacts machine uptime. Preventive care routines, such as daily lubrication and filter changes, extend equipment lifespan and help maintain the brick machine’s rated capacity.
Top Brands and Models Reviewed
Leading interlocking brick machine brands include models with different automation levels, power sources, and production capacities tailored for construction projects in Chicago.
- QT5-15 Automatic: Produces 7,200–9,600 bricks per 8 hours using 32 kW electricity. Features PLC control, hydraulic pressure, versatile molds, and a 15–25 second forming cycle. Fully automatic operation fits high-volume sites.
- LT5-10 Hydraform: Delivers increased output compared to LT4-10. Operates with a hydraulic pump for improved pressure and speed. Supports multiple mold sizes, suitable for mid-size projects.
- Lontto ECO BRAVA: Manual, diesel-powered (4 kW) unit producing 1,920–2,880 bricks per 8 hours. Uses hydraulic pressure, no pallet system, and compact manual operation. Well-suited for small construction sites or off-grid locations; $2,800 price point.
- Lontto ECO BRB: Larger manual diesel unit (5.5 kW). Yields 3,840–5,760 bricks per 8 hours, forming bricks in 5–10 seconds. Cost-saving for regional contractors with moderate output needs; $3,200 unit cost.
- LT2-40 Manual: Human-powered design outputs 1,280–1,440 bricks per 8 hours. Requires no electricity or fuel. Simplicity, affordability ($800–$1,000), and easy mobility appeal to rural or low-resource jobsites.
- Henry 40-ton: Fully automatic with hydraulic compression. Height adjustment from 190 mm to 100 mm suits specialty block requirements. Automated feeding and block delivery improve production for commercial builds.
Lontto in Chicago supports these machines with training and commissioning services, streamlining setup and operator competency for local contractors. All models use durable molds and can handle local material blends, ensuring cost savings and high-quality interlocking bricks.
About Lontto
Lontto, located in Chicago, IL, is a leading manufacturer specialising in block and brick making machines.
Under the leadership of CEO Chao Zhang, Lontto offers a wide range of products, including concrete block machines, mobile block making machines, and compressed earth block machines. The company also provides services such as installation and training to ensure the efficient operation of their equipment, helping clients achieve high-quality production with ease.
Contact:
Chao Zhang, CEO
Phone: 708 260 8300
Email: [email protected]
Website: www.block-machine.net
Location:
4992 S Austin Ave, Chicago, IL 60638, USA
Frequently Asked Questions
What is an interlocking brick machine?
An interlocking brick machine is a device that produces bricks with precise edges so they fit together without the need for mortar. These bricks are formed using hydraulic or mechanical compaction, ensuring uniform strength and density.
How do interlocking bricks improve construction efficiency?
Interlocking bricks speed up construction by allowing quick assembly without mortar, reducing labor and costs. Their precise fit also ensures straighter walls and less material waste, resulting in faster project completion.
What materials are used in interlocking brick production?
Common materials include sand, cement, stone powder, fly ash, gravel, soil, and water. These can often be sourced locally, making production flexible and environmentally friendly.
What are the environmental benefits of using interlocking brick machines?
Interlocking brick machines help reduce mortar and water usage, lower construction debris, and maximize local material utilization. This makes the construction process more sustainable and less damaging to the environment.
How many bricks can an interlocking brick machine produce per shift?
Depending on the model, interlocking brick machines can produce between 2,000 and 7,200 bricks in an 8-hour shift, with higher outputs for fully automatic machines.
What types of interlocking brick machines are available?
Machines come in manual, semi-automatic, and fully automatic models. Manual machines are best for small projects, while automatic models suit larger, commercial-scale operations.
How much does an interlocking brick machine cost?
Manual machines typically cost $1,500–$3,500. Semi-automatic models range from $3,500–$6,000, while fully automatic machines can be $6,000–$10,000 or more, depending on capacity.
Are interlocking bricks structurally strong?
Yes, interlocking bricks have high compressive strength and provide enhanced seismic resistance due to the elimination of weak mortar joints, resulting in more durable structures.
What maintenance is required for interlocking brick machines?
Regular maintenance involves upkeep of hydraulic pumps, electrical components, and pressing molds. Routine inspections and timely replacement of worn parts can extend the machine’s lifespan and maintain performance.
Does Lontto provide support and training for these machines in Chicago?
Yes, Lontto offers installation support, operator training, and after-sales services in Chicago, ensuring local contractors can set up and use their machines efficiently.
Which interlocking brick machine is best for a small project?
For small projects, manual models like the LT2-40 or Lontto ECO BRAVA are ideal. They are affordable, easy to use, and require minimal resources.
Can these machines use local materials for brick production?
Yes, interlocking brick machines are designed to utilize local materials like soil, sand, and gravel, helping reduce costs and environmental impact.
What output can I expect from a fully automatic interlocking brick machine?
Models like the QT5-15 Automatic can produce 7,200–9,600 bricks in an 8-hour shift, making them suitable for large or commercial construction projects.
How does automation improve brick production?
Automation increases speed, consistency, and output, lowers labor needs, and reduces errors, ensuring uniform brick quality and streamlined workflows.
What support agreements are available for Lontto machines?
Lontto offers service agreements that include scheduled inspections, preventive maintenance, and fast replacement parts support to help keep your machine running smoothly.