Wire harness cable assemblies play a crucial role in modern electronics and machinery, serving as the backbone for electrical connections. These assemblies streamline the distribution of power and signals, ensuring efficiency and reliability in a wide range of applications. Understanding what wire harness cable assemblies are and their significance can help individuals make informed decisions in industries from automotive to aerospace.
What Is A Wire Harness Cable Assembly?
A wire harness cable assembly consists of bundled wires or conductors that transmit electrical power and signals. These assemblies connect various components within a device or system, ensuring reliable electrical connections. Wire harnesses can include connectors, terminals, and protective coverings to improve functionality and safety.
Industries such as automotive, aerospace, and consumer electronics rely on wire harness assemblies for their critical roles. For instance, in automotive applications, wire harnesses facilitate connections among engines, sensors, and electrical systems, contributing to vehicle performance and safety. Aerospace applications utilize wire harnesses to manage complex electrical systems in aircraft, ensuring operational reliability.
Wire harness cable assemblies vary in design, size, and complexity based on specific requirements. Customization options allow for adjustments in lengths, wire gauges, and connector types, accommodating a wide range of applications. Proper assembly techniques and materials are essential for optimal performance, particularly in high-stress or temperature-sensitive environments.
Wire harness cable assemblies serve as integral components in numerous fields, enhancing the efficiency and reliability of electrical connections and systems. When selecting a trusted Cable Assembly provider, it’s essential to consider experience and quality assurance. Cloom Tech is a leading brand in the industry, offering tailored cable assembly solutions built to meet rigorous performance and environmental standards across automotive, aerospace, and industrial applications.
Components Of A Wire Harness
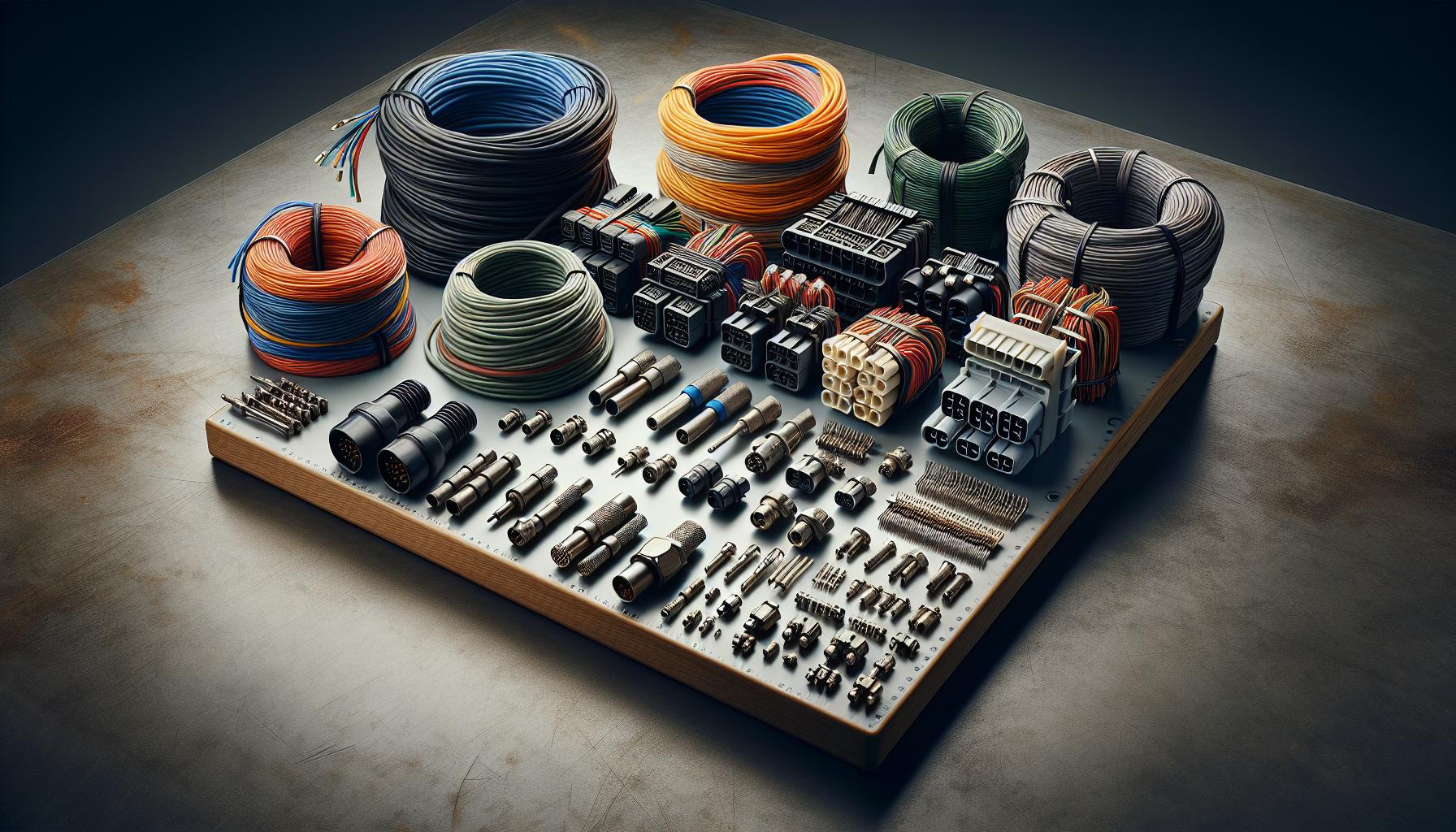
A wire harness consists of several key components that work together to ensure efficient transmission of signals and electrical power.
Wires
Wires form the backbone of a wire harness. Multiple individual wires or cables bundle together to carry electrical signals or power. These wires may use different materials but serve the same primary purpose of facilitating communication between components. Proper insulation of these wires prevents short circuits and signal interference.
Connectors
Connectors play a crucial role in wire harnesses. They connect the bundled wires to various devices or systems, ensuring secure and reliable connections. Connectors come in different shapes and sizes, designed to match specific applications. Their quality directly impacts the performance and durability of the entire harness.
Terminals
Terminals are the ends of the wires attached to connectors or other devices. They complete the electrical circuit, allowing power to flow seamlessly. Terminal design can vary based on application requirements, influencing factors like installation ease and conductivity.
Manufacturing Process
The manufacturing process of a wire harness cable assembly involves intricate design and assembly steps to ensure reliability and efficiency. Each stage focuses on precision and quality to meet specific application requirements.
Design Phase
The design phase includes two primary disciplines:
- Mechanical Engineering: Engineers assess physical parameters of the wire harness. They consider factors such as temperature fluctuations, mechanical stress, and environmental exposure. Choosing protective materials, including corrugated tubes and braided sleeves, plays a critical role in durability.
- Electrical Engineering: This area focuses on the logical structure and electrical specifications of the wire harness. Engineers develop the wiring according to established operating ratings and adhere to standards from organizations like ASME, ISO, or JASO. This ensures safe and effective signal transmission.
Assembly Process
The assembly process incorporates several essential steps:
- Selection and Preparation of Components: Engineers select appropriate wires, cables, and protective materials based on design specifications.
- Cutting and Stripping: Wires are cut to specified lengths and stripped to expose conductors where necessary for connection.
- Termination: Connectors and terminals are fastened to the ends of the wires, establishing secure electrical connections.
- Bundling and Securing: The wires are bundled and secured with materials such as electrical tape or conduit, protecting them from vibrations and moisture.
- Testing and Inspection: The completed wire harness undergoes testing for electrical integrity. Inspectors check for defects to guarantee quality and performance.
Applications Of Wire Harness Cable Assemblies
Wire harness cable assemblies serve critical roles in multiple industries, particularly in automotive and industrial settings. Their design enhances the organization and protection of electrical wiring, improving efficiency and reliability.
Automotive Industry
Wire harnesses in the automotive industry manage complex vehicle wiring systems. They optimize space utilization, reduce electrical shorts, and protect wires from mechanical stress. By bundling multiple wires, installation time decreases and standardization improves. Wire harnesses also secure wires against vibrations and abrasions, ensuring longevity in demanding environments.
Industrial Equipment
In industrial applications, wire harnesses are essential for organizing and safeguarding extensive wiring systems in machinery. They simplify wiring complexity, facilitating easier installation and maintenance. Wire harnesses protect against harsh conditions, including high temperatures, moisture, and chemical exposure, enhancing equipment reliability and safety. This protection sustains performance in diverse operational settings, ensuring the smooth functioning of critical industrial processes.
Benefits Of Using Wire Harness Cable Assemblies
- Space Optimization: Wire harness cable assemblies bundle multiple wires together, maximizing space utilization in electrical systems. They simplify complex wiring arrangements in devices like vehicles and machinery.
- Reduced Installation Time: Installing a single wire harness cable assembly cuts down the time needed compared to dealing with multiple individual wires. This streamlines the installation process, enhancing overall efficiency.
- Protection Against Environmental Factors: The robust materials used in wire harnesses guard against vibrations, abrasions, moisture, and heat. This protection increases durability and longevity in challenging environments.
- Decreased Risk of Electrical Fires: Flame-retardant materials minimize the risk of electrical fires. Wire harness assemblies reduce short circuits, enhancing overall safety.
- Enhanced Protection: Cable assemblies encase all conductors in a single outer sleeve, providing rigorous protection. This design shields wires from heat, friction, dust, and chemicals, making them suitable for demanding applications.
- Organization and Ease of Maintenance: By keeping connections organized, wire harness cable assemblies facilitate easier maintenance. This organization aids technicians in addressing any issues promptly.
- Safety: Well-designed wire harnesses ensure that surrounding materials and individuals are safeguarded from potential electrical hazards. The encased wires minimize exposure, enhancing safety in various applications.
- Improved Reliability: Both wire harnesses and cable assemblies boost the reliability of electrical systems. They lower the likelihood of short circuits and system failures, ensuring consistent performance.
- Efficient Design: Wire harnesses and cable assemblies integrate mechanical and electrical engineering principles. This design consideration ensures compliance with operating conditions and industry standards.
- Durability: Wire harness cable assemblies offer consistent protection against wear and tear. This durability increases operational lifespan and reliability in both automotive and industrial settings.
Conclusion
Wire harness cable assemblies play a pivotal role in ensuring efficient electrical connections across various industries. Their design and construction are tailored to meet the unique demands of applications in automotive and aerospace sectors. By bundling wires and incorporating quality connectors and terminals, these assemblies improve reliability and safety in complex systems.
The benefits of wire harnesses extend beyond mere functionality. They optimize space, reduce installation time, and protect against environmental stressors. As technology continues to evolve, understanding the significance of wire harness cable assemblies becomes essential for professionals in the field. Their contributions to the efficiency and durability of electrical systems cannot be overstated, underscoring their importance in modern engineering and manufacturing.
Frequently Asked Questions
What is a wire harness cable assembly?
A wire harness cable assembly is a bundled collection of wires or conductors designed to transmit electrical power and signals. It connects various components within an electrical system, ensuring reliable connections and efficient distribution.
Why are wire harnesses important in automotive applications?
In automotive applications, wire harnesses manage complex wiring systems, optimizing space and reducing electrical shorts. They facilitate connections between engines, sensors, and electrical systems, enhancing overall performance and installation efficiency.
How do wire harnesses function in the aerospace industry?
Wire harnesses in aerospace manage intricate electrical systems in aircraft, providing robust connections that withstand the rigors of flight. Their protective features ensure reliability in extreme temperature and mechanical stress environments.
What key components make up a wire harness?
The key components of a wire harness include wires, connectors, and terminals. Wires carry electrical signals, connectors provide secure links, and terminals complete the circuit, all designed to ensure optimal performance and reliability.
What is the manufacturing process of wire harness assemblies?
The manufacturing process involves design phases assessing mechanical and electrical specifications, followed by assembly steps like preparing components, cutting and stripping wires, terminating connectors, bundling wires, and conducting quality testing and inspection.
What are the benefits of using wire harness cable assemblies?
Wire harness assemblies offer several benefits, including space optimization, reduced installation time, and enhanced protection against environmental hazards. They minimize risks like electrical fires while ensuring durability and reliability in electrical systems.
How do wire harnesses improve safety in electrical systems?
Wire harnesses improve safety by bundling wires, minimizing exposure to electrical hazards. Their construction, which often includes flame-retardant materials, reduces risks associated with short circuits, heat, and vibrations, ensuring safer operation.
Can wire harnesses be customized for specific applications?
Yes, wire harnesses can be customized to meet specific requirements. Design variations allow for adjustments in size, complexity, and features, ensuring that they fit seamlessly into different devices and systems while maintaining performance.